FILL YOUR CUP!
During the spring Atlanta scouting visit w the BAP board (the “U.S. EC”), I was inspired to extend our hosts’ southern hospitality beyond hugs and enthusiastic welcoming.
I hope you enjoy your handmade, porcelain cup - made especially for you as a BAPlanta 2024 participant.
Please fill your cup with your beverage of choice - be it coffee or tea, or that rum and coke from the swag bag.
You can…
… drink hot or cold from your cup;
… microwave your cup.
… put your cup in your dishwasher.
… see how your cup was made on this page.
and yes - you should!
THE US- UK POTTERY CONNECTIONS
While community-focused solar project finance law is my “job”, ceramics is my “jam.”
I made pots full-time in my 20s; I recently returned to the world of professional potters. I am the third generation of Americans studio craftspeople, trained in the tradition of Bernard Leach, a 20th century potter who settled in St. Ives in Cornwall, England. Leach’s best friend was Shoji Hamada, a Japanese potter grounded in the “mingei” folk craft movement.
My high school ceramics teacher was a student of Prof. Warren Mackenzie at the University of Minnesota, who apprenticed at the Leach Pottery in St. Ives. Many of my closest friends and mentors studied with Mackenzie; each generation of makers tries to add to the tradition with our own commitment to making daily life special through well-crafted, unique handmade ceramics.
UK BAPer Tom Knowles-Jackson is a dear friend and a full-time potter. Tom was trained in a parallel tradition of English potter Michael Cardew. The US-UK ceramics connection continues to be a special relationship of its own kind.
MADE FROM PORCELAIN
All of these cups were made from using “recycled” clay - reclaiming dried clay or trimmings from carving the feet of cups and bowls. See more about that process below. I started using porcelain clay about 4 years ago, to allow for more vibrant glaze colors, as my now-urban residence required a cleaner electric kiln; when I lived in the country and fired using wood, I used a more rugged stoneware clay with a slightly more muted pallet.
The main ingredient in my porcelain clay also has a UK connection. It is a grolleg clay - a refined, pure porcelain clay mined in the Cornwall region. I love using this smooth, pure clay and the brighter color that is visible through my current glazes.
THROWING
I threw these cups on a treadle-powered pottery wheel that I’ve used since 1994. The cups are thrown “off the hump” - centering a large piece of clay and then measuring with my hands the right amount of clay for the next cup. Each piece is unique, and this fluid way of throwing allows me to explore small nuances of a shape, leaving the belly fuller than the previous cup, or perhaps making the top lip of the cup reach further out than the last pot.
I let my pots show that they are handmade. In some cases that means leaving tool marks or fingerprints, and in others it means they may embody that wabi-sabi idea of imperfect beauty. They might be a bit off of round, or show an imperfection in the clay. I embrace this as a sign that it was made by a human and not a machine.
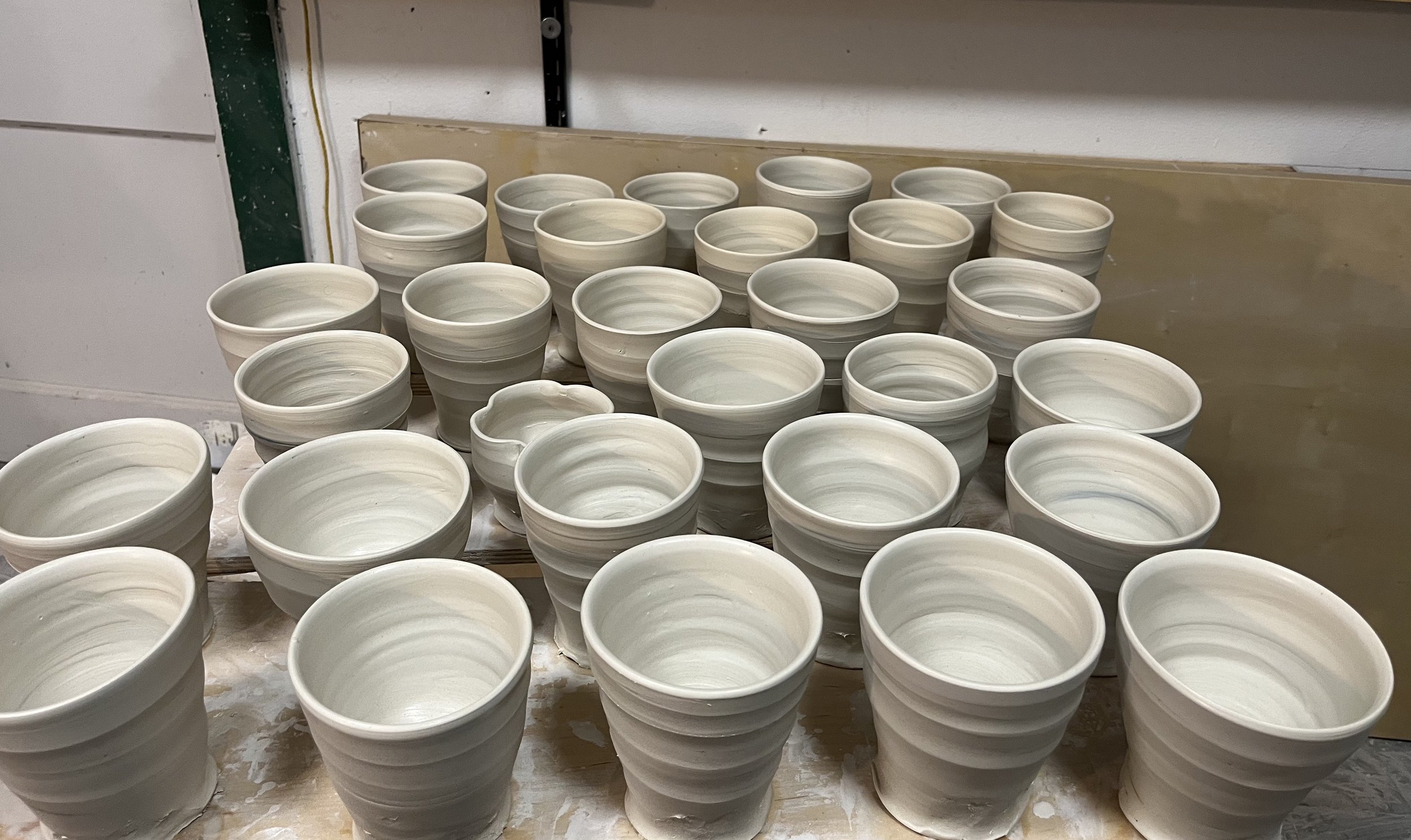
TRIMMING
After throwing on the treadle-powered pottery wheel, the cups are allowed to dry about halfway - until they are “leather hard” and can support themselves turned upside down. I try to match the outside profile with the inner shape left from throwing. I like my pots to feel “robust” without feeling heavy; I don't always find the right balance. It’s always a work in progress…
Over the decades, I have alternated between stamping my work with a “JK” stamp - and not marking the pots at all. I recently adopted the habit of impressing a more subtle mark on the bottom - see if you can guess what I used to make the mark on your cup!
GLAZING
These days, I fire pots in a “bisque” firing to about 1750 F / 950 C to make them semi-durable and become easier to handle in the glazing process.
I love the chemistry of being a potter, and have always formulated my own glaze recipes. About 5 years ago, when I decided to use porcelain and fire in the flame-less electric kiln, I had to start from scratch. I tested at least 350 different variations of base glazes and then added colorants.
These single-glazed BAP cups have been glazed by dipping in a bucket of glaze, which is a mix of clays, alkaline earths, melters (feldspars), silica (glassmaking) and some colorants (like iron oxide, cobalt, copper and chrome).
I am pleased with this current group of glazes, but I have many different small tweaks I would like to explore. Currently, the glazes are pleasing enough to be often used entirely on their own, with no additional patterning achieved by layering glazes, along with using a brushed-own wax resist pattern. As you can see on the Gallery page of this website, I do love patterning - drawn from Islamic art, American Indian patterning, fiber arts and Japanese, Chinese and Korean ceramic traditions.
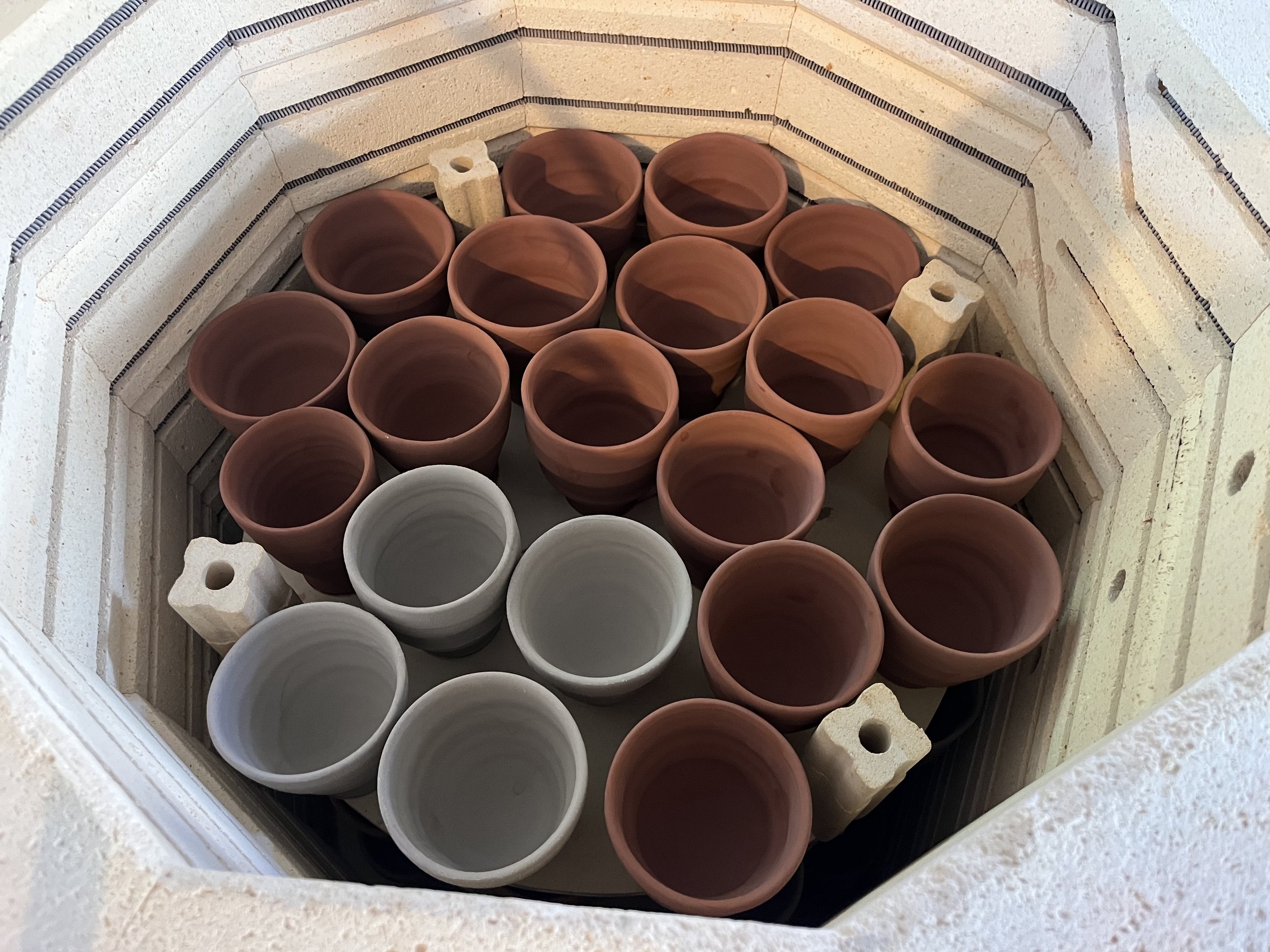
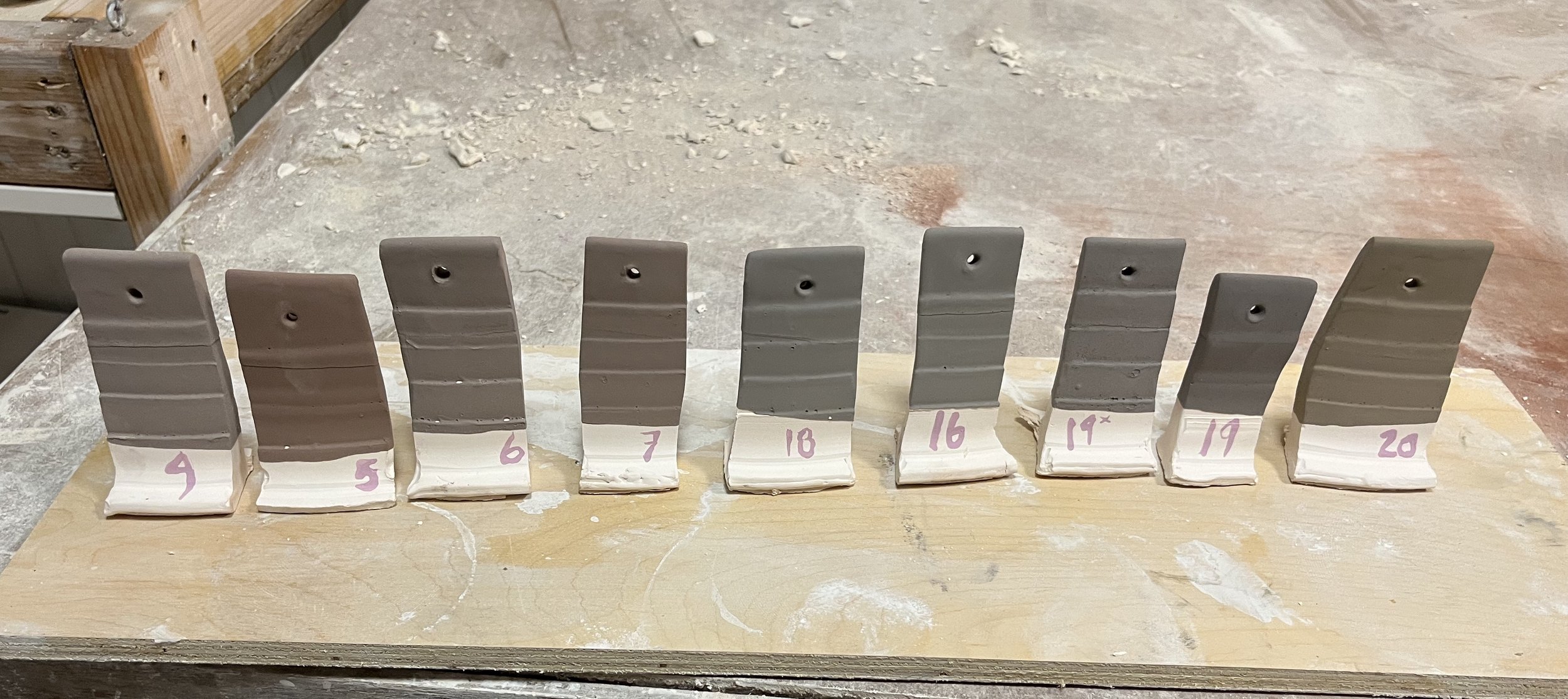
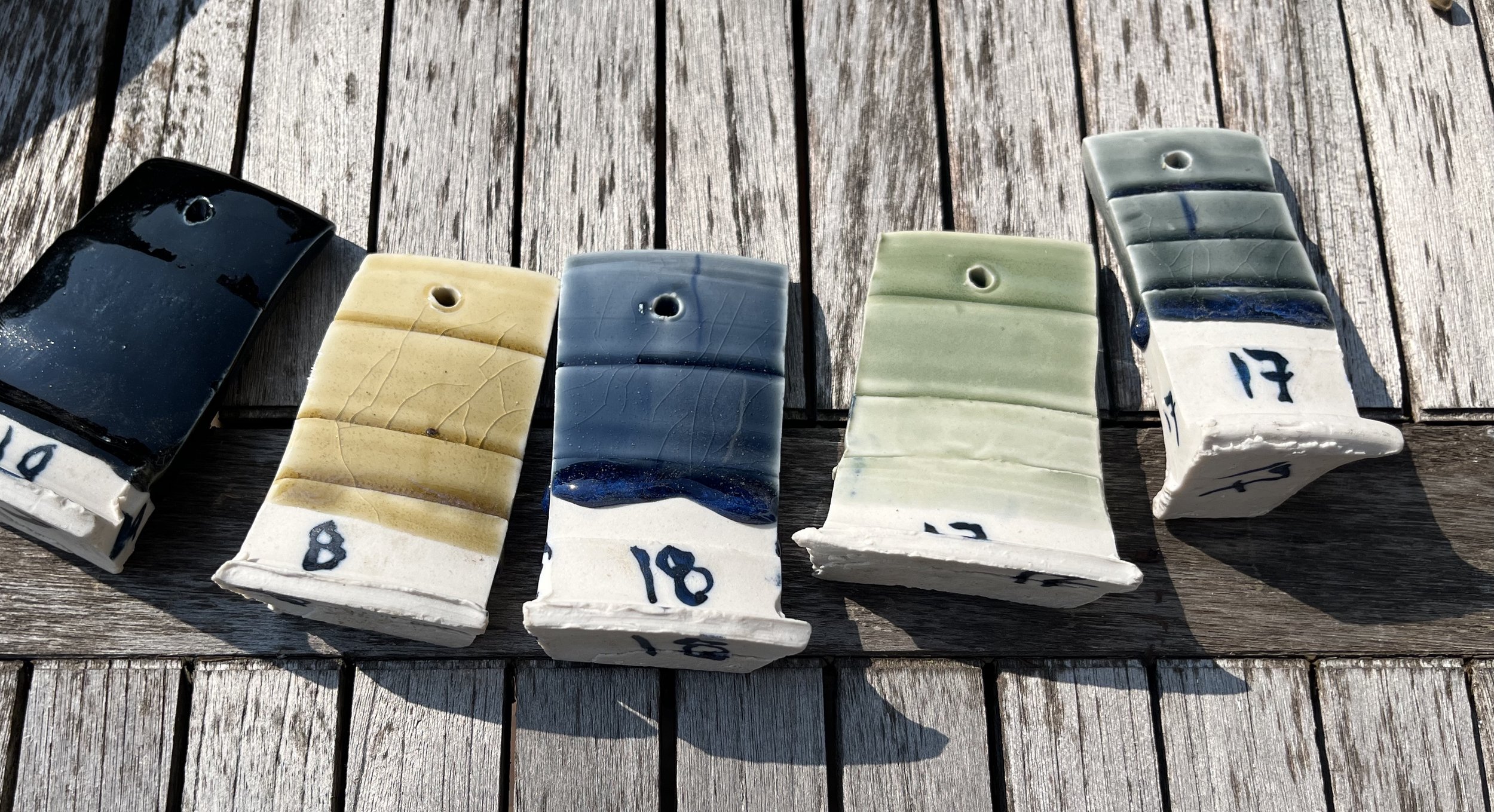
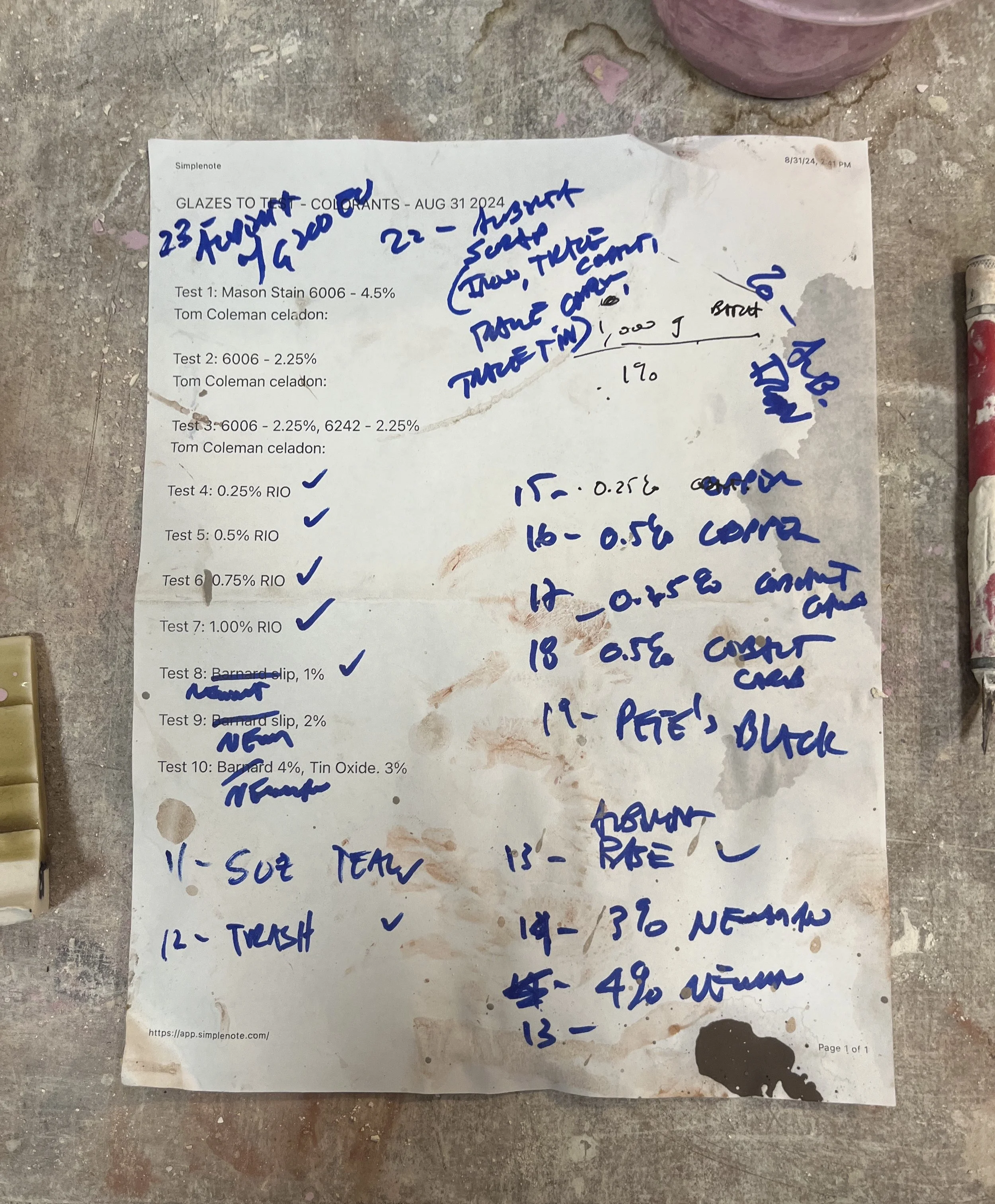
FIRING
As described above, I load the glazed cups in the electric kiln, housed in our garage which also hosts a 5.76 kilowatt solar PV system. After two decades of firing wood kilns to 2350 F / 1280 C by stoking the firebox for 18-24 hours, it’s bizarre to hit a few computer buttons on the electric kiln, and the set it and forget it.
But the mystery of transformation by fire / heat remains the same. The clay is vitrified by heat, the clay and glaze bond together, and the glaze is transformed by fire. The clean, oxidized atmosphere of the kiln makes many of my previous rich surfaces harder to obtain.
SHIPPING POTS
I try to reuse materials throughout my pottery making process. The green glaze on some of the cups is actually a “scrap glaze” made by mixing all of the leftover glazes from testing or from the bottoms of buckets, and seeing what surprise will bring with each different scrap glaze.
For shipping, I hoard boxes, bubble wrap, old amazon packaging materials and whatever other packing materials arrive at our house and for many neighbors who save materials for me as well.
All of the shipping materials used for these BAPlanta cups were reused materials - a fun challenge!
RECYCLING CLAY and STARTING A NEW CYCLE
Pottery-making is a cycle of making, trimming, drying, glazing and firing, then starting again. I take the unfired trimmings from previous cycles of making and soak them in water before using a drill mixer to make a cohesive “goop” about the consistency of thick yogurt.
I pour the reclaimed wet clay slop onto a drying rack, where it can take 3-10 days to evaporate enough water to become workable. I knead the clay to make it homogenous and to remove any trapped air.
Then, it’s time to start making pots again!
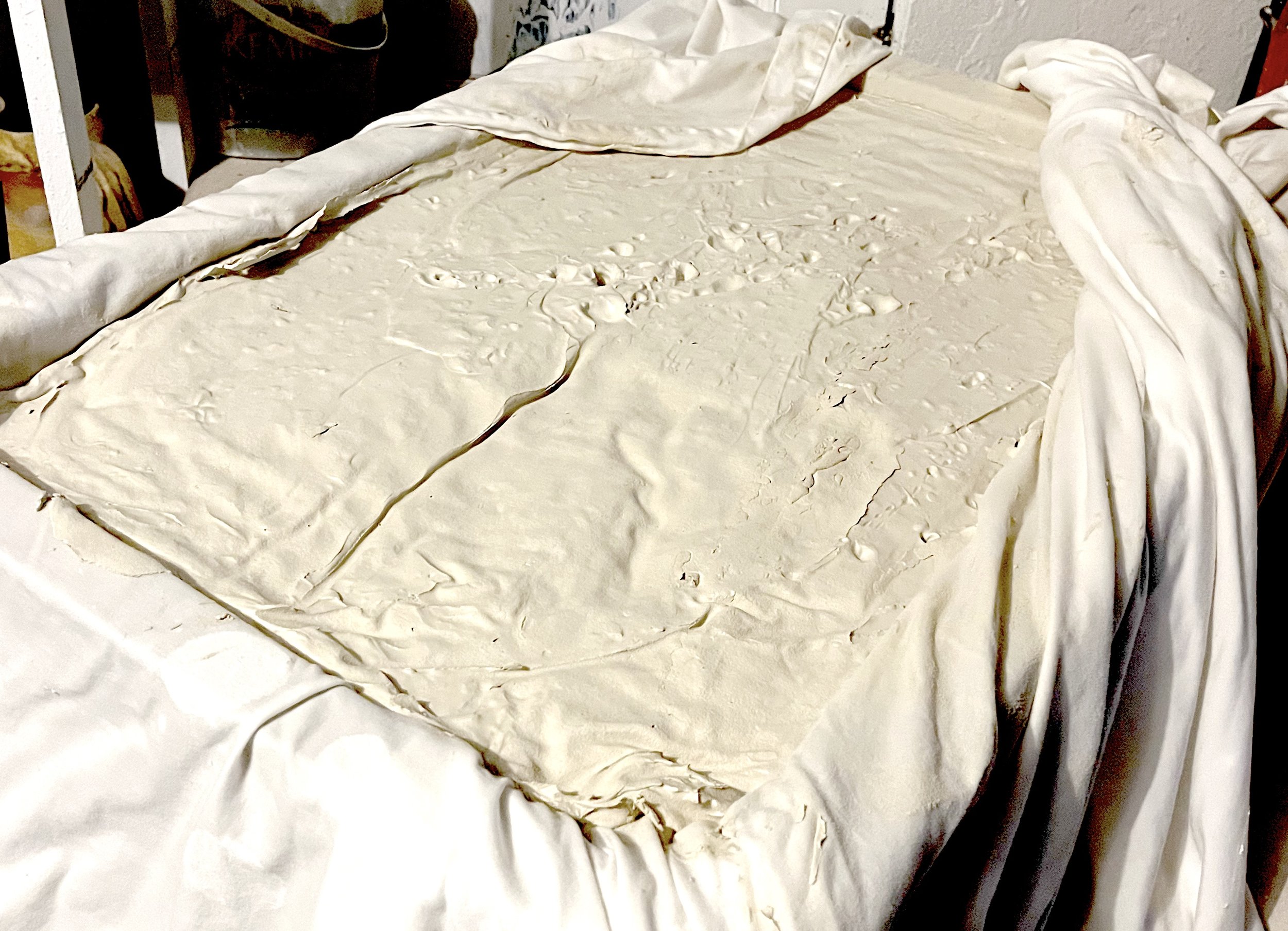
WANT TO BUY OTHER POTS TO JOIN YOUR HANDMADE CUP?
Please check out the Store - pottery makes for lovely holiday gifts for family, friends - and especially for yourself!
I can easily ship to the U.S. - and see me for details on shipping to the U.K. etc.
ENJOY YOUR CUP - BOTTOMS UP!
Jeremy